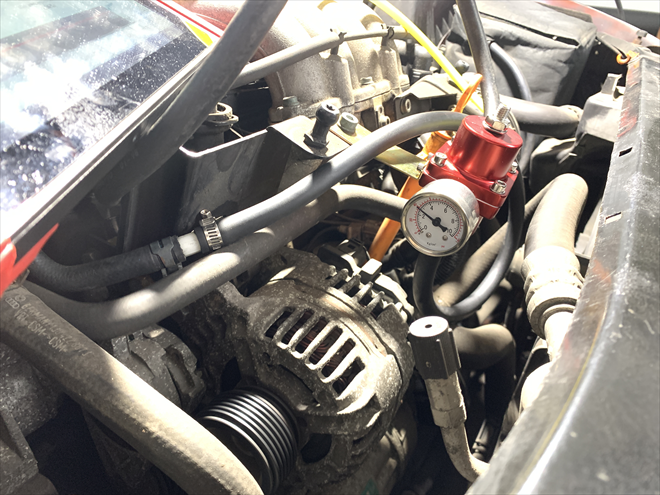
Below the article you will find two diagnostic stories of the same vehicle as they happened immediately after each other, so we will not describe the diagnostics in detail here. Because this is our company car, we could only work on it in stages in our spare time. However, we want to show how the "tips of experienced mechanics" appear in comparison with the measured and, therefore, unquestionable results thanks to the documentation. It's not that "tips" are not helpful, but they should be constantly supported by measurements...
The AQY engine of the Volkswagen Group has a few specific features and, in the past, has given trouble fixing even to real experts. We've had to think hard ourselves. As one of the first cars with the later mandatory EOBD protocol, this AQY engine often illuminated the emissions warning light even after replacing all sorts of things. Perhaps that's why, out of desperation, we took a colleague's "tip" and replaced the airflow sensor despite our doubts. As it turned out, to no avail, the same problem on the contrary, appeared even earlier.
Specifics:
Technically, it's not a contradiction of terms. They are two different faults differing on load conditions identified by our "total fuel trim" function used by our FCD Logger. This value isn't available in EOBD. While driving, the mixture, according to the FCD Logger, is –20% leaner and at idle it's +20% richer! Both are true, and the issue illuminates the emission warning light on the cluster. The car would occasionally jerk, and sometimes the engine failed to start when cold.
The first story (https://www.fcd.eu/story/15483) describes how the Lambda sensors gave us problems. We saw the sensitivity to condensation live in the first story at the above-included link.
Once the new airflow sensor didn't "work" following a colleague's hint, we decided to investigate the famous problem of the quarter-century-old AQY engines more thoroughly and, if successful, to document the reasons for the two conflicting fault code messages.
The problem of repeated cracking of the Lambda sensor ceramics from the first story was solved by replacing the sensors with specially designed (double-walled) condensation-resistant sensors. However, the " lean mixture" and " rich mixture" messages continued to appear even after airflow sensor replacement, and that's what the second story is about here:
The air for the experimental AIR-MIX injectors of the AQY engine is taken behind the airflow sensor and close to the crankcase breather system. The crankcase breather system uses an inefficient oil vapour separator, allowing oil to reach the airflow sensor's heated film (by pulsation) and into the AIR MIX system. Wherever the oil goes, it leaves behind deposits of hard resin. The first cylinder is the most affected because that's where the air line ends. It's on the electrodes of the first cylinder spark plug where you see the most deposits. The resins also slowly clog the AIR MIX system over 200 000 km, so less and less air goes into the intake around the injectors. The mixture is thus "richer and richer" at idle due to this air loss until the control unit adjusts it to the limit of the leanest possible mixture (additive fuel trim = –17% !). Then the indicator light illuminates and the fault code "mixture too rich" is stored.
It took us quite a while to determine that the opposite message, "mixture too lean", appeared when the engine was under load due to a different problem. And through simulation, we found an issue where the differential vacuum fuel pressure regulator diaphragm didn't have the required flexibility. The fuel pump created enough pressure, but the "hard diaphragm" reduced the pressure under load so much that the control unit had to increase the fuel trim and make the mixture richer by extending the injection time (the resulting multiplicative fuel trim was +20% !).
By simulations, we could satisfy the control unit, allowing it to lean out the mixture at idle by applying false air. Initially, we were not aware that air was missing due to the blocked air mix system as a result of deposits. We fixed this issue by making the mixture richer when under load by increasing the system fuel pressure by 0,5 bar with an external adjustable pressure regulator with a new and flexible diaphragm.
The result? Both load and idle fuel trims returned to within +/– 5 % values.
The solution would be to replace the fuel rail with a new part. The rail isn't available as new anymore. So, we installed a manually adjustable vacuum-controlled pressure regulator to adjust the multiplicative trim. We cleaned the AIR MIX system supply line to fix the idle fuel trim from the deposits blocking the airflow. The cluster warning light stopped illuminating and hasn't come on anymore.
The manually adjustable fuel pressure regulator replaced the original, 24-year-old differential fuel pressure regulator with an "aged" diaphragm.
The values, shown in the graph by the black line, are calculated from the mixture's short- and long-term fuel trims and are normally shown as separate values by the EOBD protocol. This calculation of an "imaginary" but quite important trace helps distinguish the fuel trim's critical moments. It provides a guide as to which fuel trim is active at any given point in time, whether additive (idle) or multiplicative (load).
Kompletní informace na toto téma
a mnoho dalších informací najdete pod odkazy níže.
Vyzkoušejte si nás nezávazně na 14 dní zdarma.
Vyzkoušet 14 dní zdarma
Komentáře (0)
Vložit soubor